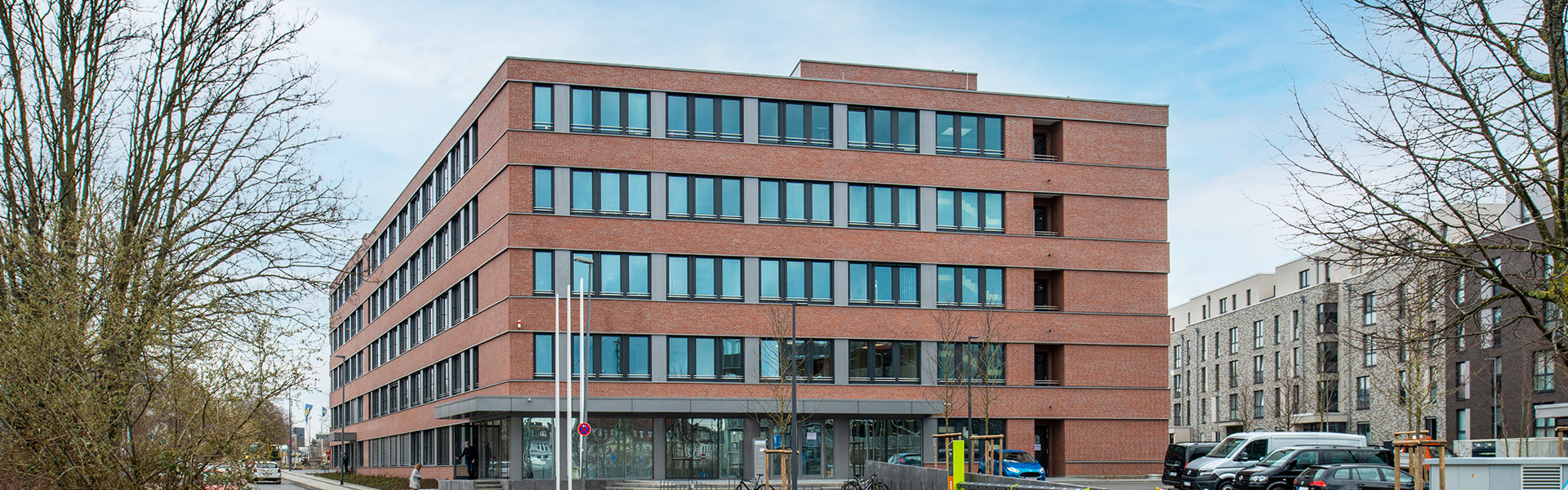
Gelungene Quartiersentwicklung in Aachen
Landmarken baut „Werkquartier am Guten Freund“ mit ALHO
Mit dem neuen Bürokomplex „Werkquartier am Guten Freund“ in Aachen vollendet die Landmarken AG erfolgreich die Umwandlung einer Militärbrache hin zur zivilen, urbanen Nutzung: Bereits 2018 wurde auf dem benachbarten, 15.500 qm großen Grundstücksteil das öffentlich geförderte und mit mehreren Preisen ausgezeichnete Wohnquartier „Guter Freund“ realisiert. Das heterogene Nutzungsangebot der Landmarken Quartiere schließt immer auch zusätzliche Angebote mit ein, zum Beispiel Kinderbetreuung, Seniorentagespflege, Einzelhandel oder Bauten für Büro und Verwaltung – so auch das neue Werkquartier 1, bei dem Landmarken erstmals moderne Modulbauweise einsetzte. Innerhalb von nur 1½ Jahren nach Auftragsvergabe stellte ALHO das hochwertige, fünfgeschossige Bauwerk fertig und setzte damit nicht nur ein Zeichen für die Schnelligkeit, sondern auch für die verlässliche Qualität der ALHO Modulbauweise.
Das sogenannte „Werkquartier am Guten Freund“ ist ein vom Aachener Büro pbs architekten entworfener Bürokomplex, der aus zwei fünfgeschossigen Bauteilen inmitten großzügiger Grünanlagen besteht. Das Besondere dabei: Obwohl beide Bauten einander gleichen, wie ein Ei dem anderen, ist das Werkquartier 1 nicht massiv, sondern aus Stahl-Modulen gebaut. Die Anforderung, dass das Gebäude schnell bezugsfertig sein musste, führte dazu, dass die Landmarken AG sich erstmals mit dem schnellen Bauen mit Modulen auseinandersetzte. „Dieses Projekt ist ein gutes Beispiel dafür, dass wir als Landmarken AG immer wieder neue Wege gehen, um die Wünsche unserer Nutzer zu übertreffen. Der frühe Einzug, der dem Mieter besonders wichtig war, konnte nur durch die Entscheidung für den Modulbau und die damit erheblich verkürzte Bauzeit möglich gemacht werden“, erläutert Arthur Kochel, Unitleiter bei der Landmarken AG.
Dabei griff das Unternehmen auf einen erfolgreichen Kontakt zu ALHO auf der Messe Expo Real zurück. „Immer mehr Auftraggeber erkennen, dass der Modulbau eine innovative, zukunftsweisende Alternative zur konventionellen Bauweise ist“, so die Erfahrung von Peter Orthen, Geschäftsführer der ALHO Systembau. „Weil unsere Bauzeiten vor Ort erheblich kürzer sind – in der Regel sprechen wir bei einem zwei- bis dreigeschossigen Bauwerk von ca. fünf bis zehn Montagetagen und einer Gesamtausbauzeit von rund drei bis fünf Monaten – rückt die Modulbauweise mit ihrem Geschwindigkeitsvorteil als Problemlöser in den Fokus.“
Arbeit im stimmigen Team
Zwar sollte im Idealfall die Entscheidung für die Modulbauweise so früh wie möglich getroffen werden, damit Architekten und Generalunternehmer bereits von Anfang an Hand in Hand planen können. Das Werkquartier 1 beweist jedoch: Auch systemunabhängige Entwürfe sind modular umsetzbar und können den architektonischen, wirtschaftlichen und technischen Anforderungen der Bauaufgabe mehr als gerecht werden. Voraussetzung dafür sind ein gutes Planungs-Team und zielorientierte, professionelle Akteure. Silvia Matschke, Mitinhaberin der ALHO Unternehmensgruppe, betont vor allem die gute Zusammenarbeit zwischen Bauherrn und Modulbauspezialisten: „Wie unsere Unternehmensgruppe ist auch die Landmarken AG ein bereits jahrzehntelang bestehendes, familiengeführtes Unternehmen. Uns einen die gleichen Werte: allen voran das Ziel, qualitätsvolle, innovative Bauten zu realisieren. Wir sind durchgehend nachhaltig orientiert und denken langfristig, nicht in Quartalszahlen. Auch darum gestaltete sich unsere Zusammenarbeit beim Projekt „Werkquartier Guter Freund“ wohl so unkompliziert und erfolgreich.“
Norbert Hermanns, Aufsichtsratsvorsitzender der Landmarken AG und seine Tochter Anke Tsitouras, ebenfalls Vorstandsmitglied, berichten: „Der Kontakt zu ALHO bestand schon einige Jahre. Als es dann an die konkrete Planung ging, haben wir uns bei Besuchen in der ALHO Raumfabrik von der Qualität der Bauweise überzeugt.“ Und auch Sylvia Friederich, Prokuristin und Mitglied der Geschäftsleitung hat diese Erfahrung gemacht: „Wir hatten tatsächlich von Anfang an das Gefühl, in ALHO einen Baupartner gefunden zu haben, mit dem wir sehr konstruktiv und auf Augenhöhe zusammenarbeiten können, der pragmatisch an die Dinge herangeht und bereit ist, mit uns gemeinsam Lösungen zu erarbeiten.“
Und so begann eine fruchtbare Zusammenarbeit, die mit der Übergabe und dem Bezug des Neubaus ein erfolgreiches Ende gefunden hat.
220 vorgefertigte Raummodule - auch außerhalb des rechten Winkels
Zusammen mit pbs architekten wurde unter der Leitung des Architekten Olaf Peters der Entwurf für das 9.600 qm umfassende Bürogebäude zügig dem ALHO Modulbauraster angepasst. Parallel zum Ausheben der Baugrube auf felsigem Grund, dem Setzen der Fundamente bzw. den Rohbauarbeiten für eine Teilunterkellerung – all das ebenfalls von ALHO projektiert und umgesetzt – ging es im März 2020 an die Vorfertigung der insgesamt rund 220 Stahlmodule. „Da der Gebäudegrundriss das Baufeld entlang der umgebenden Straßen voll ausnutzt und damit teilweise außerhalb des rechten Winkels verläuft, mussten rund 30 Stahl-Module abweichend vom Standardraster trapezförmig zulaufend konstruiert werden. Doch auch das kann unsere Produktion auf hochmodernen Werksstraßen in der ALHO Raumfabrik problemlos leisten“, berichtet ALHO Projektleiter Björn Schleifenbaum. Und – einerlei ob rechter Winkel oder nicht: Durch die integrale Planung treffen alle Fachdisziplinen von Anfang an zusammen, alle Entscheidungen werden im Vorfeld gebündelt. Ein durchgängiges Qualitätsmanagement bei ALHO stellt mit einer Reihe organisatorischer Maßnahmen sicher, dass Fehler von Anfang an vermieden werden. „Dabei werden alle qualitätsbezogenen Aktivitäten und Zielsetzungen in einer ganzheitlichen Prozesssteuerung zusammengefasst mit dem Ziel die Arbeits-, Produkt- und Dienstleistungsqualität zu verbessern und damit die Kundenzufriedenheit zu sichern – oder besser noch: zu steigern“, berichtet Schleifenbaum.
Serielle Vorproduktion bietet viele Vorteile
Olaf Peters (pbs architekten) sieht in der seriellen Vorproduktion der Module im Werk den Schlüssel für die hohe Modulbauqualität und die ebenfalls damit verbundene verkürzte Bauzeit vor Ort als großen Vorteil für die Bauherren aber auch für Architekten: „Die eingespielte serielle Produktion im Werk minimiert potentielle Fehler und bauablauf-störende Witterungseinflüsse können weitestgehend ausgeschlossen werden. Diese Produktionsweise ermöglicht eine gesteigerte Ausführungsqualität. Nach dem Aufstellen der Module steht ein bereits weit ausgebauter Rohbau auf der Baustelle, denn Fensterelemente, Trennwände und Sanitäreinheiten werden bereits ab Werk eingebaut. Vor Ort kann dann direkt mit den weiteren Ausbauarbeiten und der technischen Gebäudeausrüstung begonnen werden.“
Hochwertige Klinkerfassade
Das Werkquartier 1 schließt in seiner Mitte ein begrüntes Atrium ein – als Regenerations- und Pausenzone für die Mitarbeitenden. Dass die Modulbauweise auch in Sachen Fassadengestaltung konventionell errichteten Gebäuden in nichts nachsteht, zeigt das Bauwerk sehr deutlich, denn es wurde gestalterisch identisch zum massiv errichteten Werkquartier 2 geplant: „Keramische Klinkerriemchen in Floating-Buttering-Verfahren im sogenannten „wilden“ Verband verlegt und mit liegenden schmalen Fensterbändern gegliedert, strukturieren die großen Gebäudeflächen. Graue Alufelder lockern die strenge Fensterreihung auf und sorgen für einen spannungsvollen Materialwechsel. Die zum Atrium hin weiß verputzte Innenfassade sorgt für einen überraschenden Kontrast und eine freundliche Aufenthaltsatmosphäre“, erläutert ALHO Projektleiter Björn Schleifenbaum. Und Olaf Peters (pbs architekten) ergänzt: „Architektonisch ging es vor allem darum, eine schlichte Gleichförmigkeit oder eine rein additive Gestaltung auf Basis der Module zu vermeiden. Es sollte eben keine Assoziationen mit einem „Plattenbau“ aufkommen – Vorurteile gegenüber der Modulbauweise, die immer noch in einigen Köpfen sind. Dieses Ziel haben wir gemeinsam mit dem Bauherrn und ALHO über die Fassadengestaltung und wenige, aber wirkungsvoll gesetzte Akzente erreicht. Wir sind sehr zufrieden mit dem Ergebnis.“
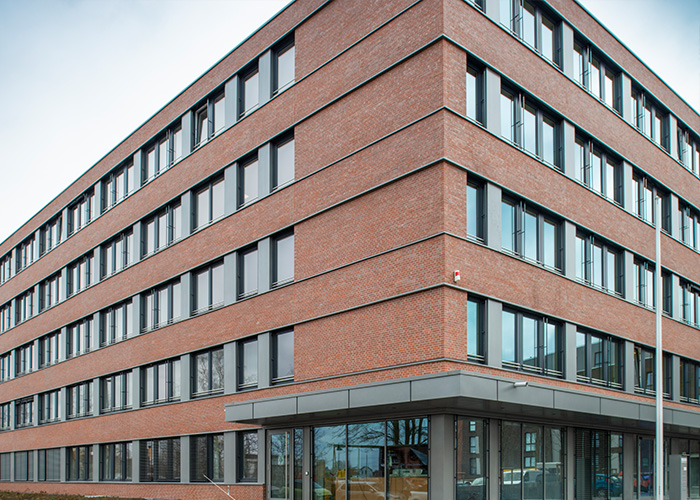
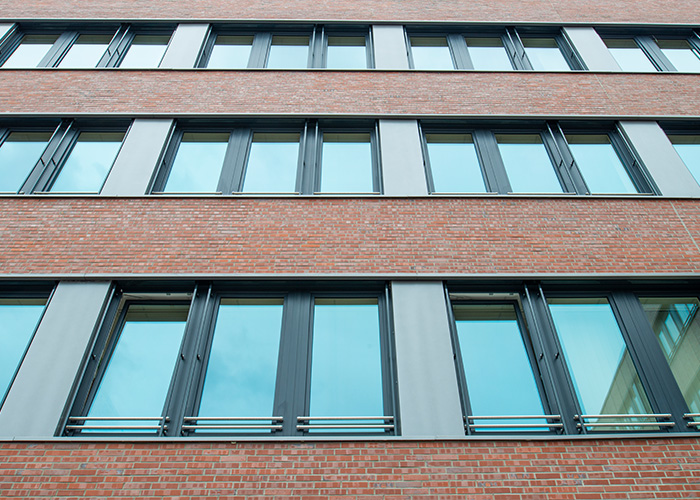
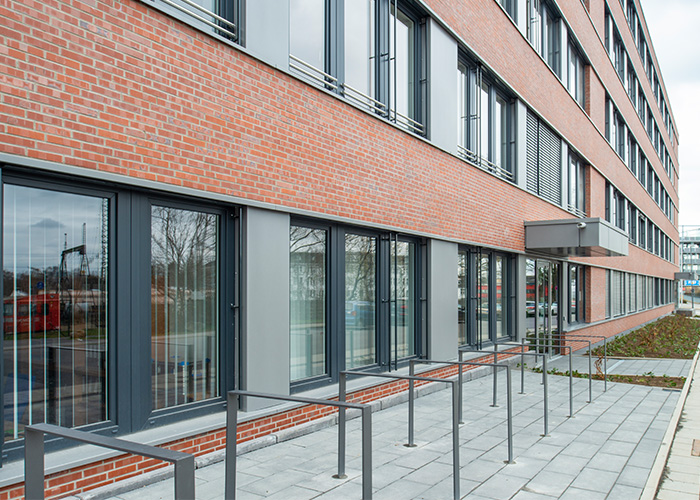
Rund 10.000 qm flexible Bürofläche
Hochwertige Materialien kennzeichnen auch die hellen, lichtdurchfluteten Innenräume des Büro- und Verwaltungsgebäudes, die mit strapazierfähigen und pflegeleichten Bodenbelägen wie Keramikfliesen, Vinyl und Nadelflies ausgestattet wurden.
„Unsere Wünsche bezogen auf Gebäudestruktur, Raumaufteilung aber auch auf die Materialqualität haben wir den Planern in einem detaillierten Raumbuch frühzeitig mitgeteilt“, berichtet Arthur Kochel und ergänzt: „Wir sind sehr zufrieden, wie diese letztendlich umgesetzt wurden. Außerdem haben wir im Sinne einer großzügigen Raumwirkung sehr stark darauf geachtet, nur wenige Stützen im Innenbereich zu zeigen.“ So beeindruckt im Erdgeschoss das über 100 qm und nahezu stützenfrei konstruierte Foyer sowohl Besucher als auch Mitarbeiter: Über eine großflächige Pfosten-Riegel-Glasfassade leitet es visuell direkt in den grünen Innenhof über. Und auch im 4. OG befindet sich an der nördlichen Gebäudespitze ein 113 qm großer ebenfalls stützenfrei konstruierter Saal. Mit seinem großen Eingangsfoyer, dem praktischen Stuhllager hinter Faltwänden, vor allem aber dem grandiosen Blick über Aachen bietet er den perfekten Rahmen für repräsentative Meetings.
Vorbereitet für die Zukunft
Drei Treppenhaus- und Aufzugsanlagen stellen die barrierefreie Erschließung der vier Obergeschosse sicher. Sie steuern bereits die derzeit noch ungenutzte Flachdachfläche des Gebäudes an, wo in einer späteren Erweiterung einmal ein Rooftop-Garden mit Flugdach für stimmungsvolle Events über den Dächern der Stadt entstehen soll. „Baulich flexibel wollten wir auch bezogen auf die Grundrissorganisation bleiben: Obwohl derzeit alle Geschosse stringent mit sich aneinanderreihenden Büro- und Besprechungsräumen und ergänzt um Teeküchen, Sanitär- und Nebenraumzonen aufgebaut sind, erlaubt das ALHO Bausystem mit seiner freitragenden Stahlskelettstruktur und den nichttragenden Wänden eine hohe Flexibilität. Innerhalb des bestehenden Mietverhältnisses oder nach Auszug kann damit die Anordnung und Organisation der Grundrisse in Teilen verändert oder sogar komplett neu aufgebaut werden“, beschreibt Artur Kochel einen besonderen Vorteil der Modulbauweise aus Sicht von Projektentwicklern und Investoren.
Schnell und unkompliziert können Wände versetzt oder geöffnet werden, auch das Aufstocken und Anbauen ist ohne viel Schmutz und Lärm jederzeit möglich. Die ursprüngliche Investition in das Bauwerk ist so unabhängig von der mittel- und langfristigen Mietentwicklung gesichert. „In der Nutzungsphase – und darüber hinaus – können Modulgebäude in Sachen Wirtschaftlichkeit besonders punkten. Über den gesamten Lebenszyklus von der Erstellung, über die Nutzung, eventuelle Umnutzung, Rückbau und Recycling weisen sie signifikant niedrigere Life Cycle Costs auf als herkömmlich errichtete Bauten“, erläutert Peter Orthen.
Nachhaltig auf vielen Ebenen
Dem stimmt auch Olaf Peters (pbs architekten) zu: „Die optimierte Modul-Vorproduktion im Werk minimiert den Ressourcenverbrauch sowie Verschnitt und Abfälle, die extrem verkürzte Bauzeit vermindert die Verkehrs- und Lärmbelastung der Umgebung. Auch Stahl als Baustoff mit seinem hohen Recyclinganteil wirkt sich positiv auf die Nachhaltigkeit aus, ebenso die potentielle Rückbaubarkeit des Gebäudes bei gleichzeitig hohem Wiederverwertungspotential der zuvor verbauten Materialien und Modulstruktur. Somit beinhaltet die modulare Bauweise wesentliche Aspekte von Cradle to Cradle bzw. eines Circular-Economy-Prinzips.“
Zudem schafft die flexible Anpassungsfähigkeit der Gebäude an den aktuellen Raumbedarf maximale Flächeneffizienz und prädestiniert die Modulbauweise für die urbane Nachverdichtung und somit für die Nutzung bereits vorhandener Strukturen – ein ebenfalls wichtiger Aspekt nachhaltigen Agierens.
Apropos innerstädtische Nachverdichtung: Auch in Sachen Baulogistik ist ALHO ein kompetenter, weil erfahrener Partner. Das zeigte sich auch auf dem knapp bemessenen Baufeld in Aachen, das nicht nur sehr wenig Platz für die Anlieferung der Module bot, sondern auch kaum Lagerfläche für Baumaterialien. ALHO arbeitete mit einem bereits im Vorfeld detailliert konzipierten Materialmanagement, das auch den Einsatz unterschiedlicher Schwerlastkräne beinhaltete. „Dass die Baumaßnahme mitten in der Corona-Pandemie umzusetzen war, stellte neben allen anderen Herausforderungen dann nur noch eine kleine zusätzliche Hürde dar, die dank effizienter Protokoll- und Hygienemaßnahmen aber keine Beeinträchtigung des Bauerfolgs zur Folge hatte“, sagt Björn Schleifenbaum abschließend. Pünktlich im Dezember 2020 konnten die Mieter einziehen.
Seite teilen: